
Once you've acquired all the materials necessary, you can start making your burning-wood art projects. There are many kinds of stencils to choose from, including Lettering, Numbering, Mesh, Graphite, and a Lettering and Numbering stencil. To create designs using oil pencils, stencils can be used. These simple steps will help you get started.
Stencil for lettering
A lettering template for burning wood has many advantages, such as a consistent design and size. The stencil is made of food-grade PET (polyethylene terephthalate), which is safe for your body and easy to clean. It protects against inhaling toxic smoke and burning. However, it is important to use a respirator as well as a safety mask when you are burning wood.
If you're unsure about which stencil to use, consider using a pencil. If you are using a pencil to trace the design onto wood, it is best to do so with heat in order not to end up creating a melted stencil. You can create an exact lettering stencil by sealing the wood. This will protect your artwork against further damage. Alternatively, you can also use a sharp knife tip or an open flame to trace the design.
Numbering stencil
The numbering stencil is a useful tool for making decorative signs or labels. These stencils are made of food-grade PET, or polyethylene terephthalate, a type of plastic. This material is completely safe to consume, odorless and reusable. It is also lightweight, durable and flexible. It is non-toxic and therefore a great choice to make decorative signage. Lowe's carries a variety of craft stencils.
These letter stencils are made of PET material, which makes them extremely flexible and washable. They are durable and easy-to-clean. The stencils are three inches square and can be repeated. They can also be reused for other DIY projects because they are reusable. You can use them for wedding showers, open houses and home decor. The stencils come with a variety of shapes and designs to fit any occasion, including holidays and birthday parties.
Mesh stencil
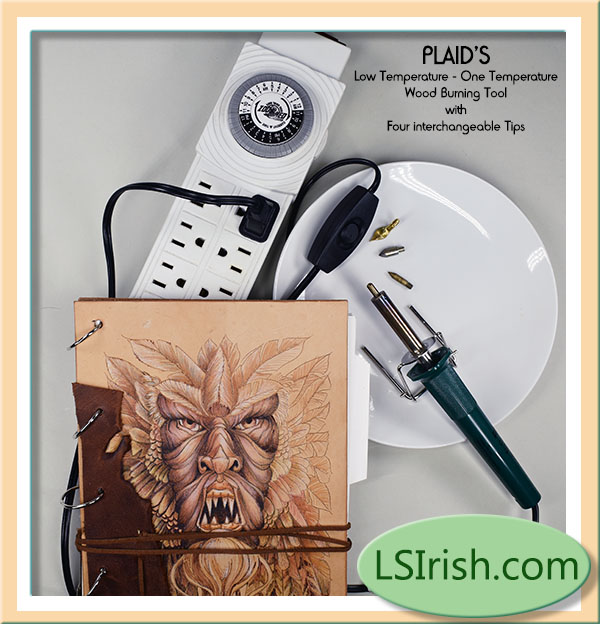
The mesh stencils will allow you to burn wood in a unique way. These stencils are available separately from Torch Paste. You will need a medium squeegee with a brush for small designs. A heat gun of at most 1000 watts will be required. The final thing you will need is a substrate.
A set of stencils and freehand tracings can be purchased. The first set of stencils you need will have a pattern. While the second set will have freehand patterns, they can be used to create your own stencils. You can also purchase a set that is designed to burn wood such as a triangle and circle. A stand is also a must, as wood burning can be messy.
You can print the stencils or make them yourself. To make a stencil you can also use a picture of an object. While the design is important, it's also important to remember that your stencil must be appropriate for the type of wood being burned. If you have a piece pine, for example, you could trace a bird on it. This is a great way to use photographs in your woodworking project.
Graphite stencil
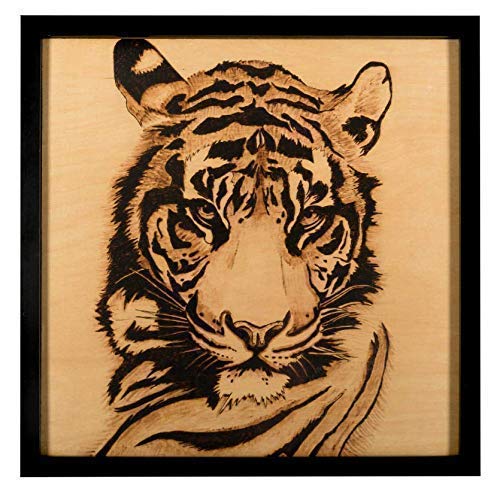
A graphite template is useful if you are looking to burn patterns or designs into wood. Online, you can find graphite stencil templates for free. These will help guide the flame as you burn the wood. Afterwards, you can remove the stencil using a damp cloth to erase the design. This stencil can be used on wood that hasn't been burned before you color it with oil pencils. However, you will need a graphite stencil before you can start.
To make a graphite template for wood burning, heat up the transfer tip. To transfer the design to wood, first heat the tip. This method is easy and works well for beginners provided that you do not burn the wood. A stencil can be used to create a design that will remain in the wood.
FAQ
What tools work best for me?
It's important to consider your preferences and needs when buying tools. Do you prefer metal or plastic handles? What size screws and nails do you use most often? Would you rather use hand tools than power tools?
Is it possible to open my own woodworking shop?
It's not easy to start your own woodworking business. There are many regulations and legal requirements that you will need to comply with. You don't have to go through all that hassle of setting it up. Many people decide to join established businesses. This way, you only need to pay membership fees and taxes.
Do I need to be a genius to succeed in woodworking?
No. Woodworking is not difficult. It is possible to learn basic tools and techniques that will allow you to create beautiful art.
How much should a woodworker charge per hour?
The hourly rate for a professional woodworker varies depending on many factors, including skill level, experience, availability, location, and other variables.
An hourly wage for skilled woodworkers is between $20 and $50.
An hourly rate of $10 for a less skilled woodworker could be possible.
Do you have any advice on how to start a woodworking business.
It's not easy to start your own woodworking business. But if you're passionate about your hobby, you won't mind putting in the effort. You might even enjoy running your own business.
When you are launching a new venture, it is important to be aware of the possibility that you will encounter unexpected difficulties. You might run out money, or you may have to borrow unexpectedly. Perhaps customers won't pay you as much as you had hoped. These situations are necessary for survival.
It is a good idea to create a separate bank account just for your company. You'll know exactly how much money is coming in by setting up a separate bank account.
Statistics
- Most woodworkers agree that lumber moisture needs to be under 10% for building furniture. (woodandshop.com)
- The U.S. Bureau of Labor Statistics (BLS) estimates that the number of jobs for woodworkers will decline by 4% between 2019 and 2029. (indeed.com)
- Woodworkers on the lower end of that spectrum, the bottom 10% to be exact, make roughly $24,000 a year, while the top 10% makes $108,000. (zippia.com)
- The best-paid 10 percent make $76,000, while the lowest-paid 10 percent make $34,000. (zippia.com)
External Links
How To
How to stain hardwood
The process of staining wood involves the application of chemicals to the wood's surface, which causes it to change its color. The wood will turn from white to brownish-red due to the chemical reaction. Oak is the most commonly used wood for staining, but other woods can also be stained.
There are many options for applying stains to wood surfaces. One method involves mixing the stain and a solvent and then spraying it on the wood. You can also apply a solution containing water and dye directly to the wooden surface. It is possible to mix stain into varnishes and paints, making it part of the finishing coat.
The first step in staining wood is preparing the surface. Cleaning the wood thoroughly removes any dirt or grease that could interfere with applying the stain. Sanding can smoothen out scratches and uneven spots. Next, you need to decide which stain you want. There are two main kinds of stains available: non-penetrating stains and penetrating. Penetrating stain penetrates deeper into wood than nonpenetrating, making them suitable for dark colors like mahogany. The best non-penetrating colors are those that work with light colors like maple.
You will need to decide on the type of stain you want to use, and then prepare your tools. The best tool for applying stains is a paintbrush. It allows you to evenly distribute the liquid over the surface. After you're done painting, make sure to have some rags handy to remove any excess stain. If you are planning to mix your stain, ensure you have enough containers for each component.
Once you have prepared your materials, start by cleaning the area where you plan to stain the wood. Use soap and warm water to remove dust and grime. Use a dampened sponge and warm water to clean the entire piece. Make sure you eliminate any loose debris, especially if you plan to stain darker wood.
Apply the stain. The stain can be applied by spraying or brushing the stain onto one end of the furniture. Work slowly and carefully, moving back and forth along the grain of the wood until you reach the opposite end. Be careful not to let the stain drip off the wood's edge. Let the stain dry completely before proceeding with the next steps.
Clear polyurethane is used to protect the painted surfaces. Apply three coats with polyurethane. Allow the third coat to dry overnight, before sanding.