
Woodworking classes for beginners can be a great way of getting started in a new hobby. It is a good place to begin by learning the basics. Students can use the projects they make for any room in the home. The projects students can do are easy enough to handle for beginners. It will also help build your confidence and be able to tackle more difficult projects in the future. You can also find plans for a Shaker Peg Rack, a small storage bin, and a wall-mounted bookhelf.
Woodturning
There are many reasons to take woodturning classes. The art and craft of turning wood is both artistic and therapeutic. This is a way to return to the roots of wood and requires the use of your mind, hands and body. As it is an easy craft that doesn't require much machinery or tools, anyone can take a class. Michael Roper, a woodturning instructor, is an excellent resource to learn the basics of this art.
Hourly classes start at $40 per session for a one hour session and $30 for two-person classes. Three-person classes are a bit more costly but you can always invite a friend, family member or colleague. Hourly classes make it easy for people living nearby and those with commitment or time constraints. Full-day classes can cost up to $425 for three students, and the three-person class is the best value if you're going to take the class with two friends.
Bandsaw box
It's a wonderful project that anyone can do in a woodworking class. It's a great way to practice bandsaw safety while building. This class is taught by Tom Wilson, a retired Industrial Arts teacher who has been teaching woodworking for over 30 years. He has also helped to build many student-built box bandsaws. For this project you will need a 6” blank and some cardstock.
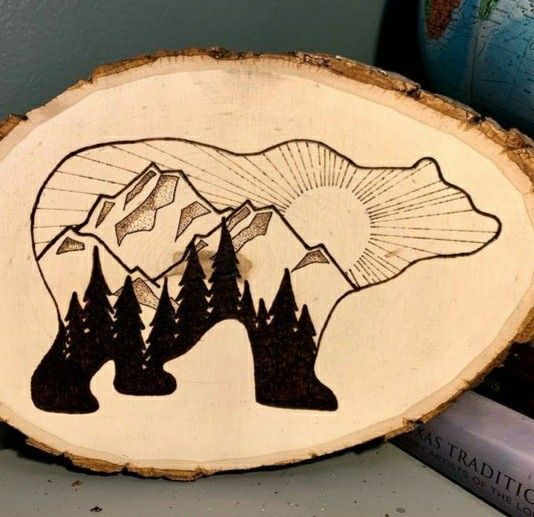
Before you begin cutting, mark your grain with a pencil. Then draw a line following it. Once you have located the grain, start to cut the line by moving straight up from the box's side. Next, you will need to cut the carcass in exactly the same direction. This ensures that the carcass is not cut in the wrong direction. The result is a rounded box which is easy to stack or stow away.
Bandsaw Spindle
Many woodworkers lack the knowledge or skills to set up their saw properly. Some may not be able to align the blade properly or to set the guide blocks correctly. The performance of a bandsaw is affected by all of these factors. You will get a smooth and straight cut with a wider bandsaw knife. A larger blade is able to cut through thicker material better. The quality of your cuts will also depend on the number of teeth in the blade. The finer a cut will be, the more tooth count on the bandsaw blade.
Bandsaw blades come in a variety of thicknesses. The stiffer and straighter your cut will become, the thicker the band. Thicker bands are more susceptible for stress cracking, but they can also breakage easily. The result is a bigger bandsaw wheel. The ideal thickness of the blade is between 4 and 6 inches. Use a knife holder to alter the direction of cuts.
Hand-carved bowls
Although hand-carving bowls in wood classes can seem difficult, if one takes the time and learns about the tools, materials, and woodworking body, they will be beautiful for many years. Ron Pickens is a retired educator and grew up in Pickens. He graduated with a BA in Social Studies at Wofford College and a MAT degree from Converse College. From 1969 to 1971, he served in the United States Army. He retired in 1999 from Pickens High School. Ron spends his spare time woodworking and enjoys teaching carving classes in Holly Springs Center.
Students will learn basic wood carving techniques and how to use traditional wooden carving tools to carve many designs. The techniques and tools used in hand carving are directly related to the shape and function of a bowl. These traditional Scandinavian traditions are often reflected in the simple lines found on hand-crafted bowls. Students will leave with a beautiful piece of handmade work to display on the dining room table.
Masterclasses in Woodworking
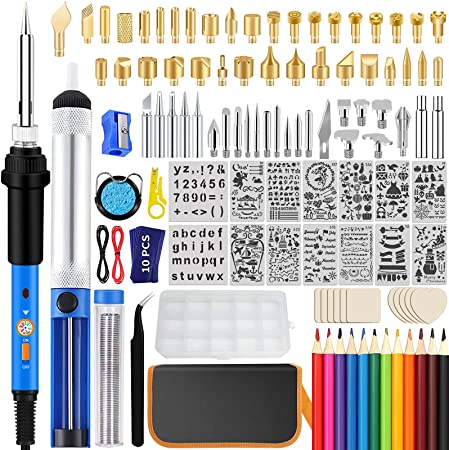
If you'd like to learn how to woodwork, you should check out woodcraft masterclasses. Woodcraft 101 provides a range of classes to help you create everything from simple furniture and intricate carvings. Each class can be purchased individually or as part of a monthly subscription that costs eight dollars. The majority of the courses cover shop basics, including how to use a router, mill lumber, and how to use a jointer and table saw. Masterclasses in woodcraft also include decorative inlay techniques.
Paul Sellers' courses for woodworking can been accessed through the Woodworking Masterclasses website. These videos provide a way to learn specific techniques and tackle difficult projects. To access the videos, you must pay a $15 monthly subscription fee. While the website is very attractive, it's missing a comment section and review feature. This is a major negative, but if you have a problem with the service, you can try a trial or free trial to see if it suits your needs.
Brooklyn Woods
Brooklyn Woods offers a seven-week course that will teach New Yorkers a valuable new skill. The non-profit, now 12 years old offers woodworking classes for jobless New Yorkers. Its students lack any education or have a limited work history. Some are even ex-inmates. Scott Peltzer, a former cabinetmaker who teaches the courses from the nonprofit's Gowanus offices.
The training program can be taken free of charge. Candidates must have strong interest in woodworking careers. You will receive extensive instruction and hands-on experience. It fosters a sense of community among students. Some students have lasting relationships. Others gain valuable life skills. It is a win-win program for everyone. Brooklyn Woods students will be able to purchase their dream home. New Yorkers are also more employable thanks to the program.
FAQ
What's the difference between a hobbyist and a professional woodworker?
Hobbyists love making things from wood while professionals are more concerned with the quality of their work. Hobbyists take great pride in their creations, and share them with family and friends. Professionals spend hours researching design ideas before starting to work on a project. They will pay attention to every detail, from selecting the best materials to finishing the project perfectly.
What is the main difference between plywood or particle board?
Plywood can be described as a mixture of layers and wood that have been pressed together with pressure. Plywood can come in many thicknesses and is used for flooring and cabinets. Particle board consists of sawdust mixed and resin. The resin is then compressed into large blocks. This board is commonly used in home improvement projects. Both boards are strong and can be easily cut.
How much money do you need to get going?
There are no exact numbers because every project is different. But if you want to get an idea of how much money you'll need, consider these factors:
-
Material cost
-
Tools and equipment
-
Time spent on the project
-
Hourly rate
-
How much profit do you expect to earn
-
Hire help
You might start small if you are just starting out. As you gain experience, more difficult projects will become possible.
How can a woodworker start making money?
Many people are beginning to learn how build furniture to launch an online business. But if you're just getting started building furniture, there are other ways to earn money besides selling on Etsy. You can sell at local craft fairs. Or you could offer workshops for others who want to learn how to build their own furniture. If you have the experience to be a carpenter, builder, or a designer, you may consider offering your services in remodeling homes or creating custom pieces.
Statistics
- In 2014, there were just over 237,000 jobs for all woodworkers, with other wood product manufacturing employing 23 percent; wood kitchen cabinets and countertop manufacturing employing 21 percent. (theartcareerproject.com)
- If your lumber isn't as dry as you would like when you purchase it (over 22% in Glen Huey's opinion…probably over 10-15% in my opinion), then it's a good idea to let it acclimate to your workshop for a couple of weeks. (woodandshop.com)
- Most woodworkers agree that lumber moisture needs to be under 10% for building furniture. (woodandshop.com)
- The U.S. Bureau of Labor Statistics (BLS) estimates that the number of jobs for woodworkers will decline by 4% between 2019 and 2029. (indeed.com)
External Links
How To
How to drive a nails in wood
When driving a nail into wood, it is important to first choose the correct size and kind of hammer. Claw hammers include mallets, claw hammers (sledgehammers), mallets, ball-peen hammers, hatchets, and mallets. Each type of hammer comes with its advantages and disadvantages. A claw hammer is best for hitting nails or hard objects. However, it can be difficult to pinpoint exactly where the blow will land. A sledgehammer allows you to hit large areas simultaneously, but it is too heavy and cumbersome to use for small tasks.
After selecting the right hammer, you will need to place your hand flat against one side of the head. The handle should rest comfortably in your hands. Hold the handle in your hand, but don’t force it too hard that you break. Hold the hammer straight up, keeping your wrist relaxed. Next, swing the hammer toward the ground and aim for the nail's center. The impact of the hammer hitting the nail should be felt. If you're having trouble getting the hang of swinging a hammer, practice with a block of wood until you get the rhythm down.
You can now drive the nail by holding the hammer to your body. You will need to position the nail so it is parallel to the wood. Keep your attention on the tip. Then, swing the hammer forward. Next, follow the motion of your hammerhead. This can be repeated several times to increase the speed of your swing. Try adding power to your swings when you've mastered the technique. Then, raise the hammer from your shoulder to bring it down. You'll have more energy to work with.
After you have nailed the hole, take the hammer off the nail. Use a pry bar or screwdriver to pull out the rest of the nails. To avoid splitting the wood, make sure the nail heads are not touching the board's surface.