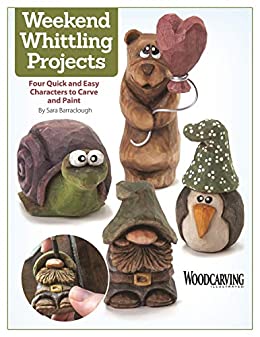
Chip carving begins with imagining where you want the blade to point. Cut the tile starting at the point and working your way to the larger chips. Do not pull out the chips, but instead gently wiggle them. You can cut the tile a little deeper if bits are still attached to the tile. You will continue to do this until the tile appears finished. Next, create your own chip carvings by using a pattern.
Free form carving
You can carve an image using a split blank or a straight-edged gouge for free-form chip carving. Because of its straight fibers, the split blank can be used to increase your carving power. You can then cut in both directions by cutting flat the top layer of the wood and removing the bottom layer. Try out different templates to improve your carving and make your own designs.
While carving is a time-consuming process, the rewards of mastering the techniques are well worth the effort. The creation of a design can take twice as long as the actual carving. Chip carving usually involves many ridges and cuts, and the "sharpness" at the bottoms of the ridges is crucial. The "sharpness of the ridges, regardless of whether you are carving a circle or not, is crucial.
Using angled cuts
It is important to imagine how your chip will look if you use an angled blade to cut it. Two sides will likely be present on the chip, with one being straight. The cut should be made with your point at the intersection of two straight walls. The third side should be cut at the lowest point.
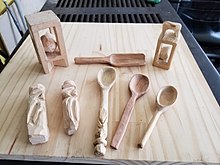
Chip carving works best with lighter wood. This allows for more contrast between the positive spaces and the negative ones. A lighter wood color will allow for greater contrast in shadows. Straight chips will highlight the negative space above them, while angled chips will create a subtle shadow that will appeal to the eye. It will appear that the letters have been cut from the wood if your chip is angled.
Flexcut knives:
A Flexcut knife can be a great option if your goal is to get started chip carving. These American-made knives feature a sharpened edge and are pre-sharpened. However, they need to be regularly stropped in Flexcut Gold polishing material. The ideal angle for this knife's bevel is 15 degrees. To carve chips, hold it at this angle.
The Flexcut knives can be a great tool for chip carving if you're not a pro at it. Each Flexcut carving knife comes with a dependable, long-lasting edge and ergonomically shaped wood handles. These knives provide precise control over each cut and reduce the chance of chipping. Flexcut offers a special coating which prevents chipping to protect your carving tools.
A pattern is made
Draw a pattern for a chip carving design. You can make a pattern that is free-form, or use basic geometric shapes such squares, ovals, or circles. It is crucial to keep the lines straight. It might take a few attempts before you get the hang of it. By making a practice piece of scrap wood, you can learn the pattern. Once you have a pattern, you can start carving!
To carve a square, draw a grid. This will allow you to experiment with different designs, creating unique pieces. You will need a pencil or ruler to draw the pattern. Each cell in the grid should be square. Also, the sides should be 3/16" - 1/4". To make triangles you can connect each corner of a cell to another to create triangles.
Getting started
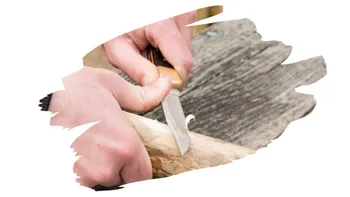
Start chip carving by understanding the basics. Most designs are geometric, so you can use graphite paper to trace a pattern on your wood. To ensure accuracy when you trace along the wood's edge, you can use an eraser or ruler. You can also use a hard pencil or eraser to remove the traced lines. After mastering this technique, you will be able to practice it on a larger surface until your grip is good.
One of the best things about chip carving is that it is incredibly easy to learn and doesn't cost much. Chip carving is far more simple than other wood carving skills. Chip carving can be used as an artistic outlet for creating beautiful pieces by beginning carvers. You can even create personalized pieces for gifts or use in your home. This is a great hobby that can be passed on from generation to generation. You can begin by practicing your chip carving techniques on a small piece of wood, such as a wooden spoon.
FAQ
What material would your recommendation be to learn woodworking?
Start with softwoods such as pine and poplar. You will feel more comfortable with these softwoods, so you can move onto hardwood.
Can I make a living doing this?
Yes! Many woodworkers do. According to the U.S. Bureau of Labor Statistics' (BLS), in May 2012 the median annual wage of woodworkers was $34,000 This is significantly higher than the national average, which is $31,000 per year.
Where can I begin with woodworking
Building furniture is the best way to learn how furniture is made. You'll need tools, and you'll have to make mistakes along the way, but if you keep at it, you'll eventually figure out what you're doing.
You should first choose the project you wish to complete. It can be as simple as a small box, or as complex as a complete entertainment center. Once you've decided on a project, find a local woodworker who specializes in that kind of work. Ask him or her for advice on what tools you'll need and where to find them. Perhaps you could ask if there is someone else who does this type of work.
Is it possible to refinish your own furniture?
Yes! You don't have to hire a professional to refinish furniture. There are many ways you can do it yourself. Here are some suggestions:
Sandpaper can be used to remove stains and scratches. Then wipe down the surface with a clean cloth.
Apply clear polyurethane finish. Allow to dry completely before moving furniture.
Use acrylic paint to paint furniture.
Instead of using paint, stain is a better choice. You can give your furniture a rich appearance with stain.
Shellac wax is applied. This will protect and shine the wood.
Which wooden products are most popular?
The most successful wooden items are made from sustainable wood.
The most popular types of wood for furniture include oak, maple, cherry, mahogany, walnut, and teak.
These woods are extremely strong but also have beautiful colors and grain patterns. They are also very durable if properly maintained.
To protect wooden furniture from moisture damage, you should paint it first. All surfaces should be painted, including doors, drawers, and handles.
If you want to make sure that your furniture lasts as long as possible, then you should choose a paint that is resistant to water.
Followed by two coats, you should apply a quality oil-based primer. Depending on how often it will be worn, you may need to apply several coats.
Spray cans or aerosol paints should be avoided. These products contain solvents that evaporate quickly and leave behind harmful fumes.
Statistics
- Woodworkers on the lower end of that spectrum, the bottom 10% to be exact, make roughly $24,000 a year, while the top 10% makes $108,000. (zippia.com)
- Average lumber prices rose about 600 percent between April 2020 and May 2021. (familyhandyman.com)
- The best-paid 10 percent make $76,000, while the lowest-paid 10 percent make $34,000. (zippia.com)
- If your lumber isn't as dry as you would like when you purchase it (over 22% in Glen Huey's opinion…probably over 10-15% in my opinion), then it's a good idea to let it acclimate to your workshop for a couple of weeks. (woodandshop.com)
External Links
How To
How to make wooden joints
This tutorial will help you join two pieces of wooden together. We will be using the "pocket-hole joint", which involves drilling holes in wood and then gluing them together. This method is great if your wood's straight and smooth. You may want to consider other methods, such as dowel joining. These are the steps
-
Drill Pocket Hole Joints. Start by measuring and marking the spot where the pocket hole joint will be placed. Then drill 3/4 inch deep holes into the ends of each piece of wood using a jig saw or handheld drilling machine.
-
Sand Smooth. Sanding the wood's edges will help ensure that the joint won't split later.
-
Glue Together Apply glue on both sides of the wooden plank. Allow it to cool for at least 5 minutes before you attach the pieces.
-
Secure the pieces together. After the glue has dried you can attach the pieces to form a flush joint.
-
Trim Joinery. Trim any excess wood surrounding the joint once the glue has dried completely.
Be sure to leave enough space between each piece so that they can be turned inside-out.