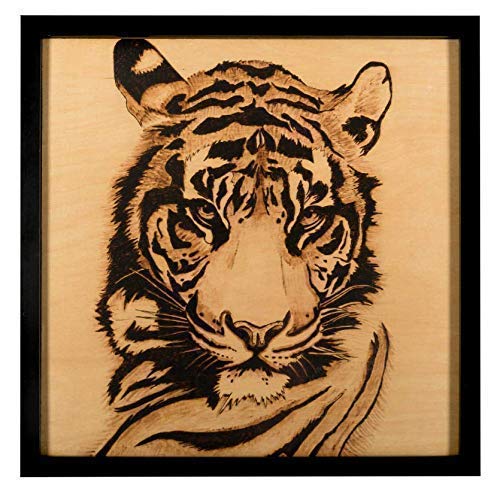
If you are looking to create beautiful and custom pieces for home, you might be interested learning more about pyrography. This ancient art dates back to the 17th century, and is the process of burning intricate designs and decorations into wood. The resultant burn marks make beautiful dark designs. This can include landscapes as well as portraits. This technique has been in use for centuries and is still a popular choice when it comes to home decor.
Yoko sugi ban
The technique of shou sugiban, which is charring wood's surface, was developed in Japan in the 18th century. This creates a rich charcoal-black color on the wood's exterior, which can also give it an Alligator skin or cracked appearance. Japanese cedar is a popular choice for a rustic, traditional look. Other wood species are possible with varying degrees. This controlled charring process is a great preservation technique that strengthens the wood and prevents future damage.
Shau sugi ban
The way char is removed is the main difference between shou suugi ban and traditional sanding. Woodworkers who use shou sugi ban sandpaper or wire brushes to remove the charred layer on the top layer of the wood are able to scrape it off with wire brushes. Either way, you need to scrape enough char away to reveal the brownish-black color underneath. The result will look like an alligator's skin, so sanding is essential to remove any excess char.
Shau sugi ban on cedar
While shou sugi ban on pyrography creates an appealing wood finish, it has practical implications. You can track pieces of charred wooden wood throughout a building. Additionally, they can be inhaled easily by those who live within the treated space. In order to address this issue, pyrographers now use a propane torch as an alternative to traditional wood-burning. Here is a look at the differences between the two styles.
Yaki Sugi Ban on Basswood
Yokisugi ban on cedar, a centuries-old Japanese method, can increase wood's beauty as well as its durability. Although sometimes called Shou-sugi ban, the process involves charring wood to create beautiful patterns. It is so common in Japan, cedar is used for many shou-sugi ban projects. Satoshi Yamamura, the operations director of a Japanese wooden company, explains why shou Sugi Ban is so popular and what this means for woodworkers.
Yaki sugi bans blue stain pins
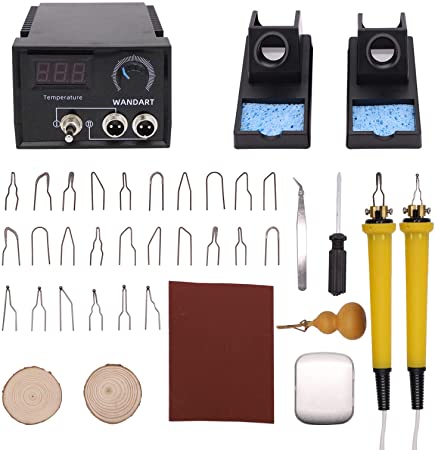
This process is also known as shou suugi ban and uses fire to preserve wood. Traditionally, cedar is used to perform shousugi ban. But other woods can also be used. Although cedar has been used traditionally for this process however, yakisugi is also possible with other woods, such as maple, Ash, and Birch. The technique is particularly popular among traditional Japanese craftspeople.
Shau sugi ban on basswood
Charring cedar pieces gives them a deep, rich black color and a unique crackled surface. Cedar is naturally water-resistant and repels pests. However, the charred surface has sculpting qualities. Untreated and reclaimed wood are available. Alternatively, a cedar panel can be treated to produce a more subtle burnt wood finish.
Shau sugi ban on jelutong
Shou sugi bans wood-pyrography. For starters, the technique enhances the natural patterns of wood. Additionally, charred wood is more durable because of the thicker carbon layer. This depends on the species of timber used and the environmental conditions in which it is being applied. Shou sugi Ban is an environmentally friendly way of treating wood.
FAQ
Is it difficult to start my woodworking business?
It can be difficult to start your woodworking business. There are many requirements and regulations that must be followed. You don't have to go through all that hassle of setting it up. Many people choose to join existing businesses. This way, you only need to pay membership fees and taxes.
Can I succeed in woodworking if I'm a genius?
No. Woodworking does not require any special skills. It is possible to learn basic tools and techniques that will allow you to create beautiful art.
How much does a hobbyist need to invest in getting started?
If you're looking to start your own woodworking business, you'll probably need some capital to buy the necessary tools and supplies. The best place to start is by buying a small drill press, circularsaw, circular saw or sanding machine. These items aren't very expensive, so you won't break the bank.
What furniture can I refinish?
Yes! You don't have to hire a professional to refinish furniture. There are many ways you can do it yourself. Here are a few suggestions:
Use sandpaper for removing stains and scratches. Use a clean cloth to wipe the surface.
Apply clear polyurethane varnish. Before moving furniture, let dry completely.
Use acrylic paint to paint furniture.
Instead of painting, use stain. The furniture will get a rich look with the stain.
Use shellac wax. You can protect your wood with wax and give it shine.
What wood items do well?
Most wooden items that are best-sellers are made from wood harvested sustainably.
The most used wood types for furniture are oak, maple and walnut.
These woods are very strong, but they also have beautiful grain patterns and colors. They will last for many years, if taken care of properly.
To prevent moisture damage to wood furniture, it is important that it be painted before any other surfaces. This covers all surfaces, drawers included, as well as doors and handles.
If you want to make sure that your furniture lasts as long as possible, then you should choose a paint that is resistant to water.
A high-quality oil-based primer should be used, followed by two coats with top coat. Depending on how much wear you expect, you might need to apply more coats of topcoat.
Avoid spray cans or aerosol colors. These products contain solvents which evaporate quickly and leave behind harmful fumes.
Statistics
- The best-paid 10 percent make $76,000, while the lowest-paid 10 percent make $34,000. (zippia.com)
- Average lumber prices rose about 600 percent between April 2020 and May 2021. (familyhandyman.com)
- In 2014, there were just over 237,000 jobs for all woodworkers, with other wood product manufacturing employing 23 percent; wood kitchen cabinets and countertop manufacturing employing 21 percent. (theartcareerproject.com)
- Most woodworkers agree that lumber moisture needs to be under 10% for building furniture. (woodandshop.com)
External Links
How To
How to join wood with no nails
Woodworking is an enjoyable hobby. You can make useful items from wood with your hands, which is both relaxing and fun. However, there are times when you want to join two pieces of wood together without having to use nails. This article will show you how to do it to make your woodwork projects look great.
The first thing you'll need to do is cut off any rough edges from your pieces of wood before joining them together. You don't want to leave sharp corners that could cause problems later on down the road. Now you can start gluing the boards together.
If you are working with hardwood, only one side should be glue. For softwoods like cedar and pine, glue should be applied to both sides. Once you have applied the glue, press down on the boards until they are fully attached. Before you proceed to the next step, be sure to let the glue dry completely.
After you've glued your boards, you'll want to drill holes into the joints where you plan to insert screws. The size of these holes depends on what type of screw you choose to use. For example, if your screw is a 1/2-inch wooden screw, drill a hole that is at minimum 3/4 inches deep.
Once you have drilled your holes you will need to drive the screws through each joint and into the backside. Avoid hitting the board's top surface. Otherwise, you could ruin the finish. Try to not hit the ends of the screws when driving the screws. This will prevent splitting in the end grain of the wood.
You'll need to protect your completed project from the elements. You can either cover the entire furniture or just the top. You will want to choose a product that will be durable for many years. Oil-based varnishes are, among others, polyurethanes shellac, laquer, and other oil-based products.
You can find these products at most home improvement stores. You should make sure you are getting the right type for the job. Don't forget to keep in mind that some finishes are toxic. Wear protective gear whenever you are handling them.