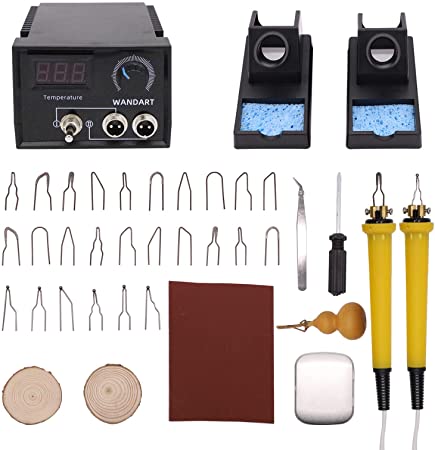
You will need a wood burning set to learn how wood burns. It includes a sponge or tin box, soldering materials, and various temperature settings. Also, you should try to make scrap materials before trying to make larger items. If you don't like the idea of burning wood, you could also buy a pre-cut piece and make your own. After that, you can start making your own decorations!
Scumbling
Grains can be applied to your project to give it a unique finish. Graining is possible in many ways. You can use a variety of metal combs or a graining toothbrush to create unique finishes. The scumble should match a ground colour. The container label or manufacturer's card will show you the right ground colour. To create a more complicated look, you can blend several methods.
You must be able to sweep in order to create realistic shapes. Sweeping refers to drawing lines slowly and rapidly. Tapered lines are the result. Scumbling, however, can be used to create texture or shading. This technique can also produce a very smooth burn. Be sure to master sweeping before trying scumbling. Combining sweeping, scumbling is the best way to get the best results. Scumbling adds an element of fun to your woodburning projects. While sweeping is important for creating realistic shapes and forms,
Dotting
Dotting wood burning is an age-old technique, dating back to medieval art. This creates a realistic edge and a shiny/opaque contrast. It is a great choice for beginners wood burning projects. Dotting requires a hot torch and a large-rounded pen tip. It is also more time-consuming than stippling and requires cleaning the tip when too much material accumulates.
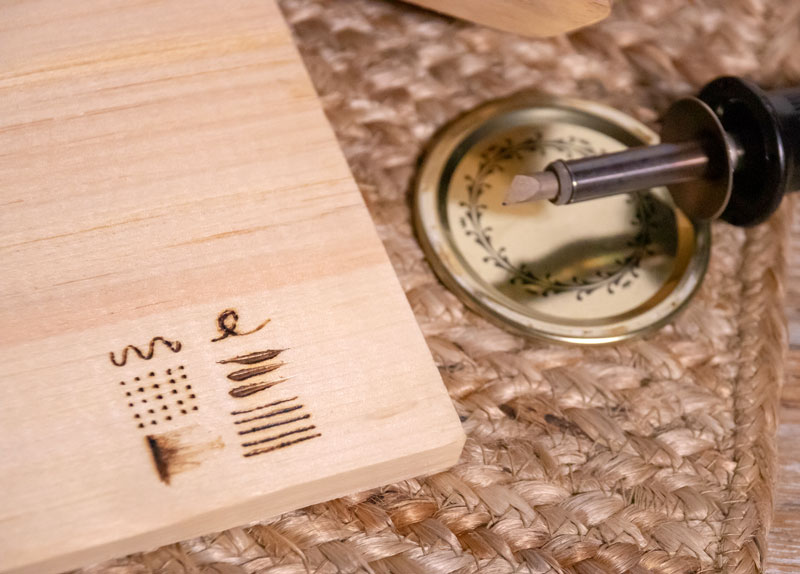
To begin wood burning with dots, follow the steps below. First, hold the pen or pencil parallel to the wood and begin with a downward motion. This technique will create straight, uniform lines. Pushing wood will create uneven lines. You can draw the dots using the same technique once you have the wood-burning tool. After the first few strokes, you will begin to practice with a lighter pressure and increase the intensity of your heat.
Shading
It is an art form to shade wood when it burns. Shaders can make images more appealing and realistic. Different wood burning techniques have different results. You can start by practicing on scrap wood to get used to them. After practice, you'll be able to create shading that will look just as great in 3D. This article will discuss several techniques for shading. The final step in shading is to choose a burnt tool.
Make sure you are comfortable. You don’t want to burn the belly. When wood burning, it's essential to avoid long lines as they can get caught in the wood and create dark areas. As mistakes can be easily repaired with sandpaper, it is best to work in small steps. When you are done, your final product will be in a perfect shape. Don't forget to take small steps so you don't burn the wood too often.
Cross-hatching
Have you ever seen a woodburning project that is beautiful? If so, you might be curious about how it was achieved. It usually involves a combination several techniques. Cross-hatching, which creates smooth gradients between dark and lighter colors, is one of the most common methods. This method is particularly useful when done with cheap wood. This technique is for anyone with any level of skill, beginner or advanced.
First, you should know how paint pens work. They are essential for anyone who is new to woodburning. These must be held in a manner that allows for you to control the tip of the pen. You should aim the tip to make contact with the wood. Next, trace the pattern using graphite. Press hard enough to draw a line. Do not repeat the same area twice.
Use a stencil

Preparing the stencil is essential before you begin wood burning. There are several kinds of stencils, including metal and plastic ones. You might want to buy a metal stencil if you're looking to create something more intricate. These stencils can be reused and cleaned easily. They are also odorless and easy to use. Once you have chosen the stencil, you can start the process of burning. First prepare your piece of wood.
A stencil can make wood burning projects much easier. They are available in many different designs and are an invaluable tool for anyone not skilled in lettering. To trace the design on metal, you can either use a stencil made of vinyl or a metal one. Either way, remember that vinyl stencils only have one use, and you will need to purchase more stencils if you want to reuse them.
Protect your work from water
After you've completed your wood burning project, you should seal it to protect it from moisture. While it's not necessary to learn complex finishing techniques to protect your wood burning work, a durable sealant is essential for professional-looking results. After sealing your woodburning job, you will need to apply the appropriate varnish. You may apply several thin coats. These steps will ensure that your item lasts a long time.
To burn your fabric, first choose a dry and well-ventilated place. Burn treated lumber or wood which has been exposed to wind and rain for a long period of time. Additionally, excessive smoke from burning wet wood is harmful and can lead to inefficient burning. Install a moisture monitor to verify that the wood has dried. It can be used to determine the wood's moisture content. Apply the linseed or coconut oil to the top.
FAQ
Do you have any suggestions for starting a woodworking shop?
It takes a lot of effort to start a woodworking business. However, if you are passionate about your hobby you will be willing to put in the effort. You'll likely enjoy the challenge of owning your business.
You should remember that unexpected issues may occur when you launch a new venture. You may run out of money suddenly. You might find customers not willing to pay the amount you expected. You must be ready to deal with such situations in order to survive.
A good tip is to open a separate bank account for your business. You'll know exactly how much money is coming in by setting up a separate bank account.
What is the difference between a hobbyist woodworker and a professional woodworker.
Hobbyists enjoy creating things out of wood. Professionals tend to focus on the quality. Hobbyists tend to take pride and share their creations with family and friends. Professionals will spend hours looking at designs before they start to build a project. Professionals will be meticulous about all aspects of their work, from selecting the right materials to finishing it.
How can a woodworker start making money?
Many people want to open an online furniture business and are learning how to build it. However, if you're just getting into furniture building, there are other options than selling on Etsy. Local craft fairs and events are great places to sell your products. You could also offer workshops to help others learn how to make their own furniture. If you have experience as a carpenter or builder, you might consider offering services such as remodeling homes or creating custom pieces for clients.
What is the minimum investment a hobbyist needs to make in order to get started?
It is likely that you will need some capital in order to buy the required tools and supplies if your goal is to open your own woodworking business. The best place to start is by buying a small drill press, circularsaw, circular saw or sanding machine. These items are affordable so you won’t break the bank.
How can my shop be organized?
To keep your workshop tidy and organized, you should first create a place for tools storage. You want your tools to stay clean and free from debris and dust. Use pegboard hooks to hang tools and accessories.
What should a woodworker be paid per hour?
The hourly rate paid to a professional woodworker is dependent on many factors. These include skill level, availability, and location.
A skilled woodworker can expect an hourly rate of $20-50.
A less skilled woodworker might charge as low as $10 per hour.
Statistics
- Most woodworkers agree that lumber moisture needs to be under 10% for building furniture. (woodandshop.com)
- Average lumber prices rose about 600 percent between April 2020 and May 2021. (familyhandyman.com)
- Woodworkers on the lower end of that spectrum, the bottom 10% to be exact, make roughly $24,000 a year, while the top 10% makes $108,000. (zippia.com)
- The U.S. Bureau of Labor Statistics (BLS) estimates that the number of jobs for woodworkers will decline by 4% between 2019 and 2029. (indeed.com)
External Links
How To
How to join two pieces of wood together without nails
Woodworking is a hobby that many people enjoy doing. It is relaxing and enjoyable because you can create something useful with wood. You may need to join two pieces without the use of nails. This article will demonstrate how to do so to preserve the beauty of your woodwork.
First, remove any sharp edges from the wood pieces before you join them. Do not leave any sharp corners as they could cause problems down in the future. After you have completed this step, you are ready to glue your boards together.
If you're working with hardwood, you should only apply glue to one side. For softwoods like cedar and pine, glue should be applied to both sides. Once the glue has dried, press the boards together until they are fully adhered. Be sure to let the glue dry before you move on to the next step.
After you have glued the boards together, drill holes in the joints where you intend to place screws. The size of these holes depends on what type of screw you choose to use. For example, if your screw is a 1/2-inch wooden screw, drill a hole that is at minimum 3/4 inches deep.
Once you have drilled your holes you will need to drive the screws through each joint and into the backside. Don't hit the board's surface. You could damage the finish. Don't drive the screws too far into the end. This will help prevent splitting of the end grain.
Protect your finished project now. You can either seal the entire piece of furniture or cover the top. You'll want a product that lasts for many years. There are many options: oil-based varnishes; polyurethane; shellac; lacquer.
These products can generally be found in any home improvement shop. You should make sure you are getting the right type for the job. Remember that some finishes can be toxic, so you should not use them indoors. Protective gear should always be worn when handling these finishes.