
It can be challenging to transport rough lumber by hand. You should always bring your hand saw, tape measure and other tools with you to the store. If the board you purchased does not fit, it is worth purchasing additional boards. Be sure to buy the board with knots and checks. You don’t want to have the board ripped and re-made. This is a wasteful way to spend your time and money.
Minimal wastage
When cutting rough lumber, a sawmill typically turns 59% of the log volume into boards. The remainder of the log can be considered waste, including sawdust, bark, chips and chips. Although a less perfect cut can result in more waste than a perfect cut, it should still not exceed 20%. Here's a simple formula to estimate the amount of wasted wood in a board. The sawmill should reduce 18% of its volume in order to get the desired lumber thickness.
One thing is that rough lumber does not come in the same dimensions. You can plan your project around the dimensions of hardwood purchased at big-box stores. This means that the edges of rough lumber are not always straight, which can lead to waste. A lot of lumber is wasted because rough-cut lumber requires a standard width. These wastes can't be recycled later.
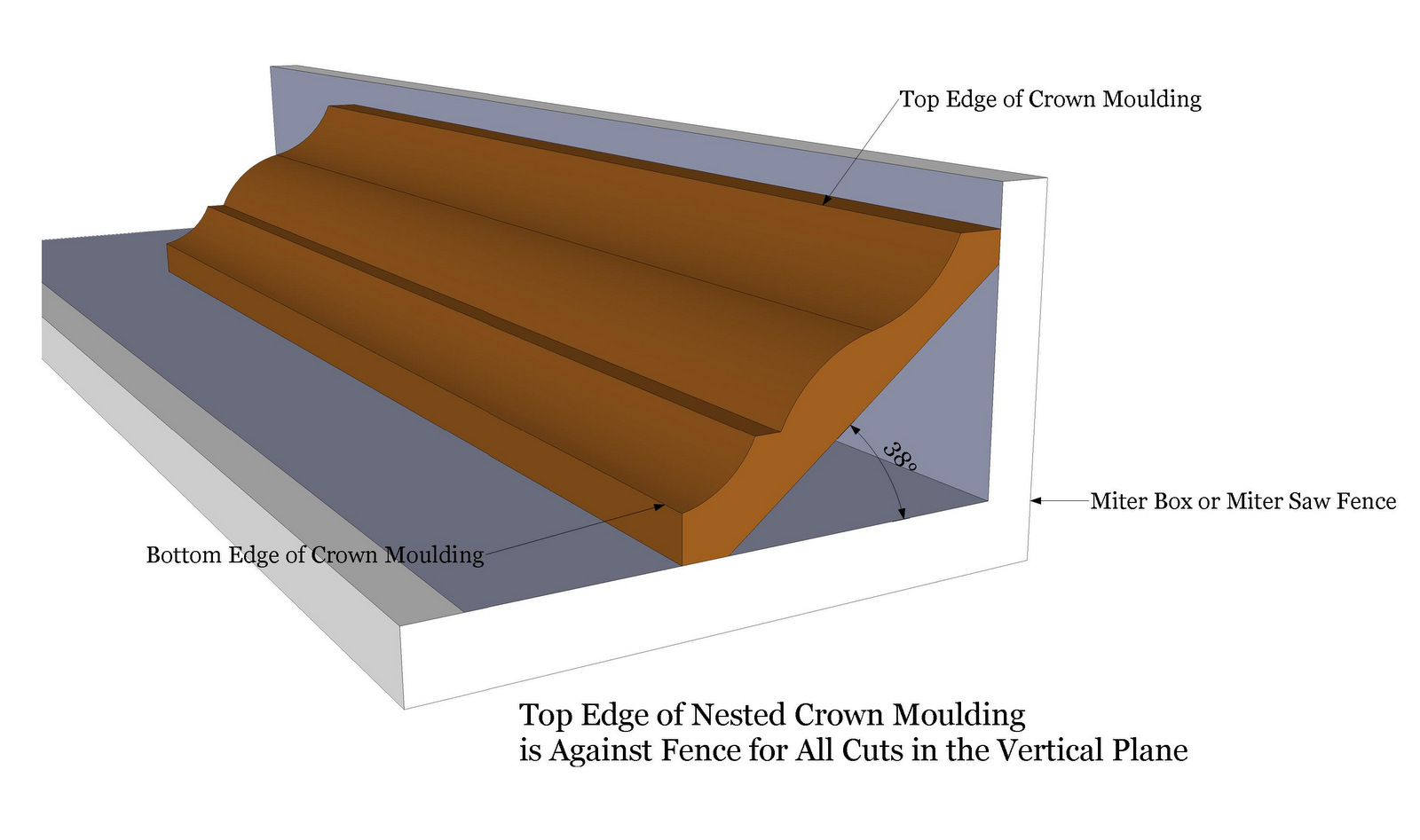
Preparation
Preparing for rough lumber cutting is as simple as measuring the material. Rough lumber may not be perfectly flat when it arrives from the lumber yard. It may not be perfectly flat and have uneven edges and faces. Therefore, it may take multiple passes to flatten. One rule of thumb is to cut 1/16" per pass. If the lumber has concave edges, you can run it through a saw with the concave side down.
It is recommended that rough-cut lumber be flattened until it is 1/4 inch thick before being cut. After flattening, plane the face to the thickness you want for the finished board. Once you know the thickness of the rough lumber measure the finished length and width. Don't forget to consider any imperfections. You should leave about a quarter inch between the boards. Then, plan your project around the available boards. You will have a difficult time working with rough lumber if it is warped, bent, or twisted.
Cost
There are two types. Dimensional lumber and rough-sawn. Generally, home improvement stores carry finished lumber but rarely rough-sawn lumber. Both types are available in lumber yards and local sawmills. The difference between the two types is in the amount of work required to process them. Because it takes less work to make, rough-sawn boards are more affordable. It is also more flexible than finished lumber in that it can be cut wider and thinner.
Purchasing lumber from a mill or lumber yard is generally cheaper, but it is less likely to come in standard lengths. Although milling your own lumber is cheaper than buying rough-sawn lumber it can still be an economical option. However, you will need to have enough shop space and more power. Milling equipment can be noisy and requires training. Zoning laws may be necessary if your mill is to be used in an area.
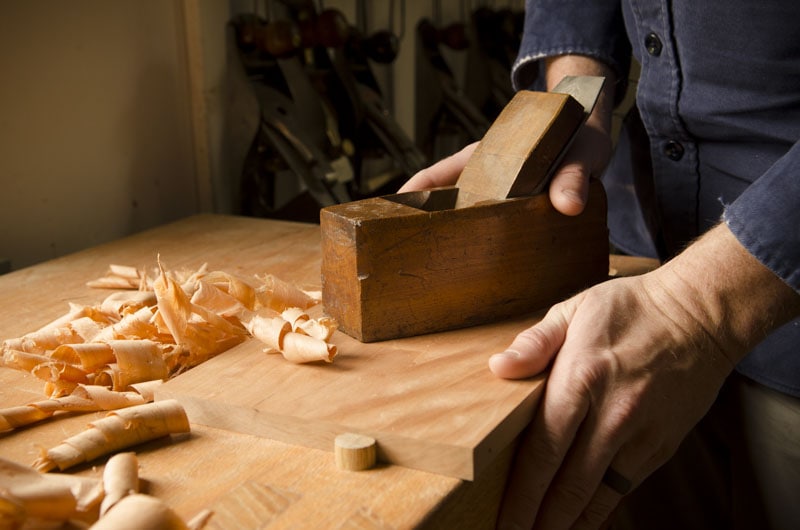
Source
When buying lumber, you have a number of options. There are many sizes, shapes and finishes available. Rough sawn lumber, for example, is unsanded and unfinished lumber that has been cut into planks. This type lumber is typically stronger than other types of lumber because it carries more moisture. However, it's also thicker then surfaced timber. These are some of many advantages to rough sawn lumber in your woodworking projects.
First, it is affordable and readily available. Rough lumber isn’t treated and is not typically sold at a hardware retailer. This type of lumber does have its advantages and disadvantages. This lumber is cheaper per board foot but less expensive by volume. Additionally, it takes longer to finish than treated lumber. If you are unsure about how much lumber to purchase, this option might be worth considering. For projects that will require rough sawn lumber, you might want to purchase a large amount and some for finishing.
FAQ
How do you calculate woodworking costs?
Remember to keep costs as low as you can when calculating project costs. It is important to ensure that you are getting the best materials prices. Also, consider all other factors that can affect the price of your projects such as skill level, experience, time and cost. Our guide to the average household DIY task price will give you an idea of how much it costs to complete different types of woodwork projects.
How often should I purchase new supplies?
You may have to replace certain tools. Hand tools will need to be sharpened regularly. If you are using power tools, you will need to purchase replacement parts regularly. To avoid buying too much at once, try to spread your purchases out over a few months.
This is a job that I can make a living from.
Yes! Many woodworkers do. According to U.S. Bureau of Labor Statistics (BLS), woodworkers earned a median annual salary of $34,000 in May 2012. This is higher than the $31,000 annual national average.
What wooden items do you sell well?
The most successful wooden items are made from sustainable wood.
Most furniture is made from oak, maple, mahogany or walnut.
These woods are strong and durable, with beautiful grain patterns. They also last for many years if cared for properly.
To protect wooden furniture from moisture damage, you should paint it first. This includes all surfaces, including drawers, doors, and handles.
If you want to make sure that your furniture lasts as long as possible, then you should choose a paint that is resistant to water.
Followed by two coats, you should apply a quality oil-based primer. Depending on how much wear you expect, you might need to apply more coats of topcoat.
Avoid spray cans or aerosol colors. These products have solvents that evaporate quickly, leaving behind dangerous fumes.
What type of wood should I choose?
Woodworking is a popular job that involves oak, pine and maple. Every type of wood is different and can have a unique look and feel that will affect the final product. Oak, for instance, is darker and harder than most other woods. Birch is lightweight and soft while mahogany is heavier and denser. You can also choose from solid wood or veneers. Veneers can be described as thin sheets of wood that have been glued together in one layer.
Is it hard to start my own woodworking business?
It is difficult to start your own woodworking company. There are many laws and regulations you need to be aware of. It doesn't mean that you have to go through the entire process of starting a business. Many people join already-established businesses. You only need to pay membership and tax fees.
What is the difference of plywood and particleboard?
Plywood can be described as a mixture of layers and wood that have been pressed together with pressure. Plywood can come in many thicknesses and is used for flooring and cabinets. Particle board can be made from sawdust, resin, and then compressed to make large blocks. This board is commonly used in home improvement projects. Both types of boards can be easily cut and are durable.
Statistics
- Woodworkers on the lower end of that spectrum, the bottom 10% to be exact, make roughly $24,000 a year, while the top 10% makes $108,000. (zippia.com)
- Most woodworkers agree that lumber moisture needs to be under 10% for building furniture. (woodandshop.com)
- Overall employment of woodworkers is projected to grow 8 percent from 2020 to 2030, about as fast as the average for all occupations. (bls.gov)
- If your lumber isn't as dry as you would like when you purchase it (over 22% in Glen Huey's opinion…probably over 10-15% in my opinion), then it's a good idea to let it acclimate to your workshop for a couple of weeks. (woodandshop.com)
External Links
How To
How to make wood joint
This tutorial will help you join two pieces of wooden together. We will be using the "pocket-hole joint", which involves drilling holes in wood and then gluing them together. If your wood is straight and flat, this method will work well. Try dowel joinery instead if your wood doesn't look straight. Here are the steps
-
Drill Pocket Hole Joints. Start by measuring and marking the spot where the pocket hole joint will be placed. Next, drill 3/4 inch holes in each end of each piece using a handheld drilling machine or jigsaw.
-
Sand Smooth. Sanding the wood's edges will ensure that the joint doesn't split.
-
Glue both sides together. Apply glue on both sides of the wooden plank. Let the wood sit for 5 minutes, then clamp it together.
-
Connect the pieces. After the glue has dried you can attach the pieces to form a flush joint.
-
Trim Joinery. Trimming the joinery after glue has completely dried.
Allow enough space between pieces so you can turn them inside out.