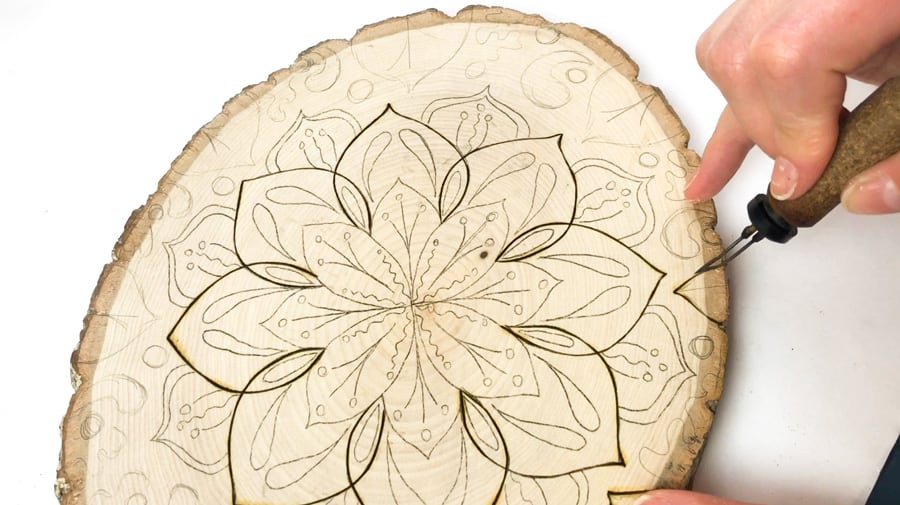
If you are looking to create beautiful and custom pieces for home, you might be interested learning more about pyrography. This ancient art involves burning intricate decorations and designs into wood. It dates back at least to the 17th-century. The resultant burn marks create beautiful dark designs. You can also include landscapes and portraits. This technique is well-known for its use in home decor.
Yoko sugi ban
A technique called shou sugiban was used in 18th-century Japan to preserve wood by charring its surface. This produces a rich charcoal black color to the wood's surface. It can also give it an alligator skin, or crack appearance. Japanese cedar is most commonly used for its rustic appearance. However, other wood types may also be used with varying degrees. The wood is protected against future damage by controlled charring, making it an excellent preservation technique.
Shau sugi ban
The way char is removed is the main difference between shou suugi ban and traditional sanding. Shau-sugiban woodworkers remove the charred layers with wire brushes. Others use coarse sandpaper. Either way, you want to scrape away enough char to reveal the brownish black color beneath. The resulting effect will be an alligator-skin-like pattern, and the sanding process is necessary to remove the excess char.
Shau sugi ban on cedar
The wood finish of shou sugi bans pyrography is attractive, but it also has practical implications. You can track pieces of charred wooden wood throughout a building. Additionally, they can be inhaled easily by those who live within the treated space. This problem is being addressed by pyrographers who are now using a propane torch to lighten the fire instead of wood-burning. Below are the main differences between the two styles.
Yaki sugi bans basswood
Yokisugi ban on cedar, a centuries-old Japanese method, can increase wood's beauty as well as its durability. Though sometimes referred to as Shou sugi ban, this process involves charring the surface of wood to create a beautiful pattern. It is so common in Japan, cedar is used for many shou-sugi ban projects. Satoshi, the operations director for a Japanese woodworking business, discusses why shou suugi ban is so popular, and what it means for woodworkers.
Yakisugi bans blue stain pine
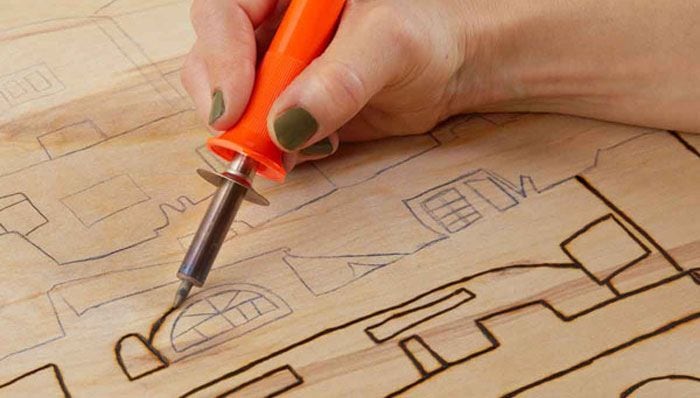
This process is also known as shou suugi ban and uses fire to preserve wood. Traditionally, cedar is used to perform shousugi ban. But other woods can also be used. Although cedar has been used traditionally for this process however, yakisugi is also possible with other woods, such as maple, Ash, and Birch. The technique is particularly popular among traditional Japanese craftspeople.
Shau sugi ban on basswood
Charring cedar creates a deep black, rich color and crackled surface. Cedar is naturally resistant and repels bugs. However, the surface that has been charred can be used to shape wood. You can choose from two types of charred wood: untreated and reclaimed. A cedar panel can also be treated to achieve a subtler burnt wood finish.
Shau sugi ban on jelutong
Shou sugi ban is a prohibition on pyrography on wooden surfaces. There are many benefits. First, it enhances the wood's natural patterns. Additionally, charred wood is more durable because of the thicker carbon layer. It all depends on the wood species used and the environment it is placed in. Shou sugi Ban is an environmentally friendly way of treating wood.
FAQ
How can I keep my shop organized?
First, make sure you have a designated space for tools storage. Make sure your tools are clean and free of debris and dust so they can be used properly. Pegboard hooks can be used to hang tools and accessories.
What would be your first step in woodworking?
Start with softwood like pine, poplar and ash. When you feel confident with these two, move on towards hardwood.
How do you calculate woodworking costs?
Remember to keep costs as low as you can when calculating project costs. You should always try to make sure that you are getting the best deal on materials. Also, consider all other factors that can affect the price of your projects such as skill level, experience, time and cost. To get an idea about the average cost for common household DIY tasks, see our guide to the average woodwork project price.
Where can I get free woodworking plans?
Woodworking plans can be found online without the need to purchase books or magazines. All you need to do is search Google. You can search Google for "free woodworking" and hundreds of websites will appear allowing you to download plans.
How can I learn basic woodworking skills
A great way to start learning how to build furniture is by building a simple bench for yourself. This project can be completed with whatever wood you have available at home. If you're not sure which kind of wood to choose, you can purchase cheap pine boards at Lowes and Home Depot. After building your bench, sand off any rough edges and apply a stain or varnish.
Is it possible to open my own woodworking shop?
It is difficult to start your own woodworking company. There are many regulations and legal requirements that you will need to comply with. However, it doesn't necessarily mean you must go through all the hassle of setting up a business. Many people opt to join existing businesses instead. You only need to pay membership and tax fees.
What is the difference in plywood and particleboard?
Plywood is made of layers of wood that are pressed together under pressure. Plywood comes with a range of thicknesses, and it is most commonly used for flooring and cabinets. Particle board is made up of sawdust mixed in resin, then compressed into large pieces. It's often used for home renovation projects. Both boards are strong and can be easily cut.
Statistics
- The U.S. Bureau of Labor Statistics (BLS) estimates that the number of jobs for woodworkers will decline by 4% between 2019 and 2029. (indeed.com)
- If your lumber isn't as dry as you would like when you purchase it (over 22% in Glen Huey's opinion…probably over 10-15% in my opinion), then it's a good idea to let it acclimate to your workshop for a couple of weeks. (woodandshop.com)
- Most woodworkers agree that lumber moisture needs to be under 10% for building furniture. (woodandshop.com)
- In 2014, there were just over 237,000 jobs for all woodworkers, with other wood product manufacturing employing 23 percent; wood kitchen cabinets and countertop manufacturing employing 21 percent. (theartcareerproject.com)
External Links
How To
How to join wood without using nails
Many people love woodworking. Woodworking can be a fun hobby because you can work with your hands to make useful objects from wood. You might want to join two pieces from the same wood, but you don't need to use nails. This article will demonstrate how to do so to preserve the beauty of your woodwork.
The first thing you'll need to do is cut off any rough edges from your pieces of wood before joining them together. Do not leave any sharp corners as they could cause problems down in the future. Once you've done this, you're ready to start gluing your boards together.
If you are working with hardwood, only one side should be glue. If you're using softwoods like pine or cedar, you should put glue on both sides. Apply the glue to the boards and press them down until they are securely attached. Be sure to let the glue dry before you move on to the next step.
After you've glued your boards, you'll want to drill holes into the joints where you plan to insert screws. Depending on what type screw you choose, the size of these holes will depend on how big they are. If you are going to use a half-inch wood screw, you will need to drill at least 3/4 inch deep.
After drilling the holes, you can drive the screws into your board's backside. You should be careful not to touch the board's front surface. This could cause damage. Try to not hit the ends of the screws when driving the screws. This will prevent splitting the wood's end grain.
Now that your project is finished, you'll want to protect it from the elements. You can either seal the entire piece of furniture or cover the top. You'll want a product that lasts for many years. Some examples include oil-based varnishes, polyurethane, shellac, lacquer, etc.
These products can usually be found at any home improvement store. Be sure to choose the right one for your project. Don't forget to keep in mind that some finishes are toxic. Wear protective gear whenever you are handling them.